Twitter Feed
Firebrand Announces 2017 Accelerated CloudMASTER® Dates
Firebrand, the leader in Accelerated Learning, has recently announced it’s 2017 delivery schedule for their accelerated CloudMASTER® training course. Delivered in partnership with Logical Operations and the NCTA, this unique…
TAP Accelerates Artificial Intelligence
Photo credit: Shutterstock Over the past few years, the use of artificial intelligence has expanded more rapidly than many of us could have imagined. While this may invoke fear and…
Cognitive on Cloud
Photo credit: Shutterstock According to the IBM Institute for Business Value the market will see a rapid adoption of initial cognitive systems. The most likely candidates have moved beyond descriptive…
Europe: NCTA CloudMASTER® Hotspot
The ongoing digital transformation continues to generate a steady demand for workers with increasingly sophisticated digital skills. This process is multi-dimensional and workers with these highly specialized skills are very…
Smart Manufacturing Is Cloud Computing
As cloud computing simultaneously transforms multiple industries many have wondered about how this trend will affect manufacturing. Often characterized as “staid”, this vertical is not often cited when leading edge…
George Youmans, Jr.: The CloudMASTER Fashionista!
So how could a NCTA Certified CloudMASTER accelerate his career in the fashion industry? To answer that question, you would need to catch up with George Youmans, Jr. He has…
Is Cloud Interoperability a Myth?
Photo credit: Shutterstock As the industry matures, cloud computing will increasingly rely on interoperability in order to grow and deliver more value to industry. Assuming this is a fact, what…
Should Data Centers Think?
As cloud computing becomes the information technology mainstream, data center technology is accelerating at a breakneck speed. Concepts like software define infrastructure, data center analytics and Nonvolatile Memory Express (NVMe)…
For Top Cyber Threats, Look in the Mirror
A recent report by Praetorian, a cybersecurity company headquartered in Austin, TX, focused on threats that resulted in data compromise or access to sensitive information. Based on a review of…
Your Choice: Cloud Technician or Digital Transformer
The CompTIA Cloud+certification validates the skills and expertise of IT practitioners in implementing and maintaining cloud technologies. This is exactly what it takes to become a good cloud technician. In…
by Kevin L. Jackson
Electronics manufacturers operate in a challenging environment. It’s hard enough to keep up with the ever-accelerating rate of change in the industry. Now customers want increasingly specialized product variations in less time and of higher quality.
Meeting this demand for increased product variation can seriously impact the bottom line. Such variability increases warranty cost that, in the US, currently averages 2.7 percent of electronics manufacturers’ revenue. This means that for every $1 billion in revenue, a company spends $27 million to support its product warranties.
Case Study: HPE Server Manufacturing Challenge
These factors explain why Hewlett Packard Enterprise (HPE), a leading manufacturer of servers and other IT hardware, is undertaking an Industry 4.0 strategy to modernize and automate assembly processes.
A key part of the process it wanted to automate is server assembly quality assurance, which was being done manually by quality operators. This labor-intensive process is prone to error due to human eye fatigue and the inability of quality operators to catch critical defects.
The company’s portfolio of server products is complex and highly customized. These characteristics made it difficult to find a machine vision system that could handle the product mix.
This situation is hardly unusual. According to Kemal Levi, Founder and CEO of Relimetrics, there is “a strong demand for computer vision to replace manual visual inspections. Yet, due to a high production variability, particularly in the case of discrete manufacturing, computer vision systems today are not able to keep up with the rate of change in configurations.â€
Quality Audit by Relimetrics
To address these concerns, HPE is implementing Relimetrics Machine Vision Systems to automate end-of-line quality inspections at their server assembly lines. The Relimetrics Quality Audit Solution for Electronics (RELI-QA) is a proven Zero Defect Manufacturing (ZDM) solution that uses machine learning to achieve a high level of flexibility and scalability for computer vision systems (see Figure 1). The solution can be rapidly deployed, trained models from one line and data can be shared across lines, and existing camera hardware can be leveraged.
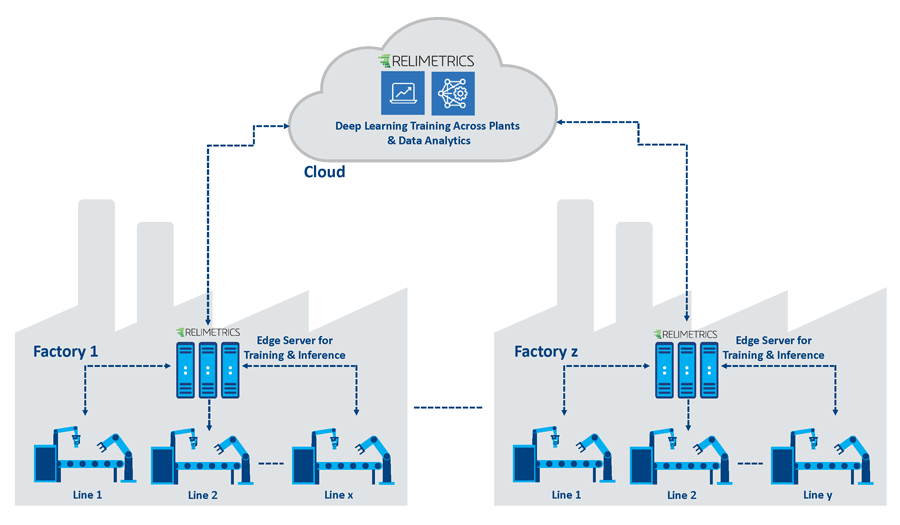
With this innovative approach to ZDM, the following can be achieved:
- 40-second inspection time for 80 components in an entire server
- Greater than 99.9 percent probability of defect detection
- 50 percent cost reduction in the company’s quality audit costs
- 80 percent cost reduction in the company’s final testing and rework
By implementing this solution, an IT electronics manufacturer producing 30,000 servers per month can reduce the cost of rework by half a million euros per manufacturing line per year. What’s more, the solution slashes the time to pinpoint the root cause of quality issues from days to minutes.
The Value of ZDM
HPE is not unique in its move toward automating quality audit (QA) as part of a larger ZDM strategy (see Figure 2).
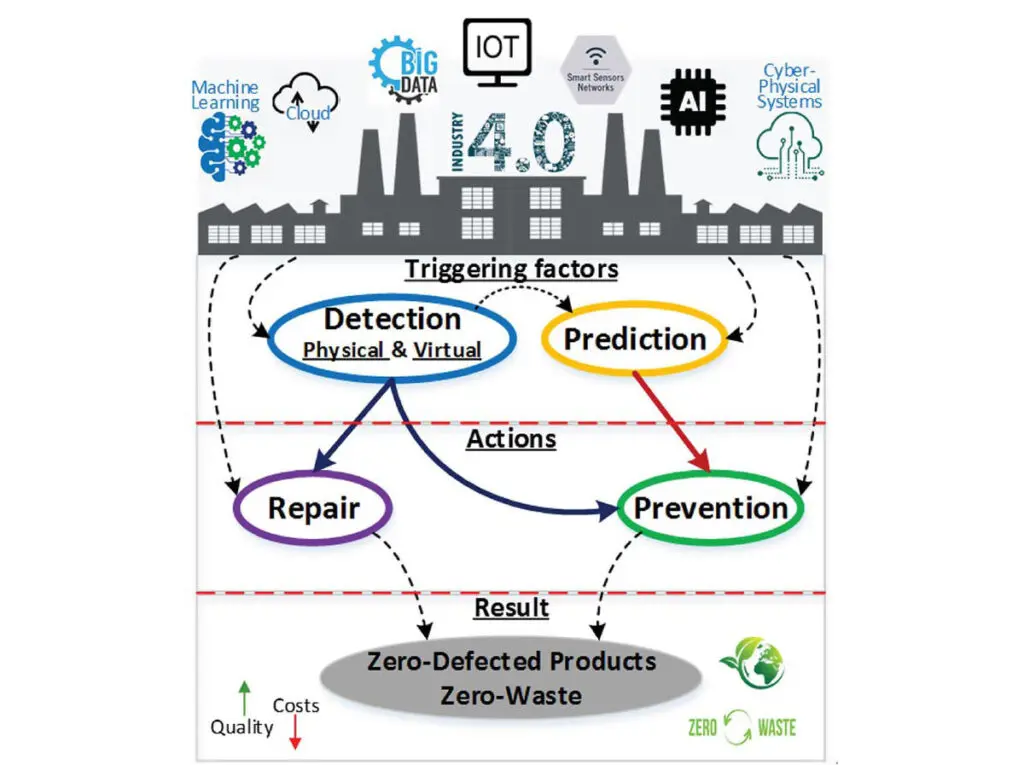
Many other manufacturers are pursuing this approach thanks to valuable aspects of ZDM such as:
- Its ability to considerably reduce the costs of handling defective products
- Removing all redundant elements within a manufacturing process
- Reducing scrap production and associated expenditures
- Continuous production supply chain improvement
- Increased safety and customer satisfaction
A recent International Journal of Production Research study stated that the evolution of Industry 4.0 has made ZDM implementation easier due to the availability of large data sets required for modern machine learning techniques. Increases in computer power and storage have combined with decreasing cost of sensors to the point that it now makes ZDM a much more cost-effective option.
A Practical ZDM Solution
The Relimetrics platform demonstrates the power of these advances. The solution can quickly evolve and adapt to changes in production parts and configurations, and enable the customer to sustain a high (>99.9 percent) level of accuracy by filtering inspection results automatically and continuously updating deep-learning models at the edge using advanced HPE edge-computing technology.
The advantage of this approach is the reduction of downtime associated with reconfiguring algorithms in high production variability manufacturing environments without any expert knowledge required. Levi explained, “Existing machine vision solutions cannot handle high production variability. Either manual intervention is required to reconfigure the algorithms or dependency on the tech vendor for updates leading to downtimes.â€
In fact, in today’s QA, the downtime associated with reconfiguring algorithms is a recurring problem experienced by many plants owned by a global manufacturer. Often, the same products or parts are being manufactured on different lines in different geographies. But these plants are not able to actively share the QA learnings with one another and take advantage of one another’s data.
Another advantage of the Relimetrics approach is its ability to leverage data produced at different lines and plants to deliver a comprehensive QA solution for a customer’s global manufacturing environment. Levi also explained, “Today, the learnings from configuration changes in, let’s say, a plant in Singapore cannot be immediately transferred to another plant in Mexico. Whereas with Relimetrics solution, the learnings from one plant can be immediately shared with another plant in another part of the world.â€
HPE Servers Inspected by HPE Servers
These ZDM accomplishments are made possible by using advanced Intel® edge-computing technologies. Running computationally intensive machine-learning calculations at the edge enables error detection accuracy of more than 99.9 percent.
In an amusing twist, the Relimetrics QA system used to inspect the server production line is itself based on HPE servers. Specifically, Relimetrics uses HPE Edgeline EL4000 servers based on powerful Intel® Xeon® processors.
But the critical contributions from Intel go beyond hardware. Levi said, “Intel provides the software and the architecture that enables Relimetrics to make the best use of their CPUs. Their technology is critical to the quality assurance solution because it enables us to run computationally intensive calculations at high speed.â€
Originally published by insight.tech on May 29, 2020. https://www.insight.tech/industry/computer-vision-advances-zero-defect-manufacturing
Sponsored by Intel Corporation
Cloud Computing
- CPUcoin Expands CPU/GPU Power Sharing with Cudo Ventures Enterprise Network Partnership
- CPUcoin Expands CPU/GPU Power Sharing with Cudo Ventures Enterprise Network Partnership
- Route1 Announces Q2 2019 Financial Results
- CPUcoin Expands CPU/GPU Power Sharing with Cudo Ventures Enterprise Network Partnership
- ChannelAdvisor to Present at the D.A. Davidson 18th Annual Technology Conference
Cybersecurity
- Route1 Announces Q2 2019 Financial Results
- FIRST US BANCSHARES, INC. DECLARES CASH DIVIDEND
- Business Continuity Management Planning Solution Market is Expected to Grow ~ US$ 1.6 Bn by the end of 2029 - PMR
- Atos delivers Quantum-Learning-as-a-Service to Xofia to enable artificial intelligence solutions
- New Ares IoT Botnet discovered on Android OS based Set-Top Boxes